Vital Stops to Keep your Buses Moving Profitably
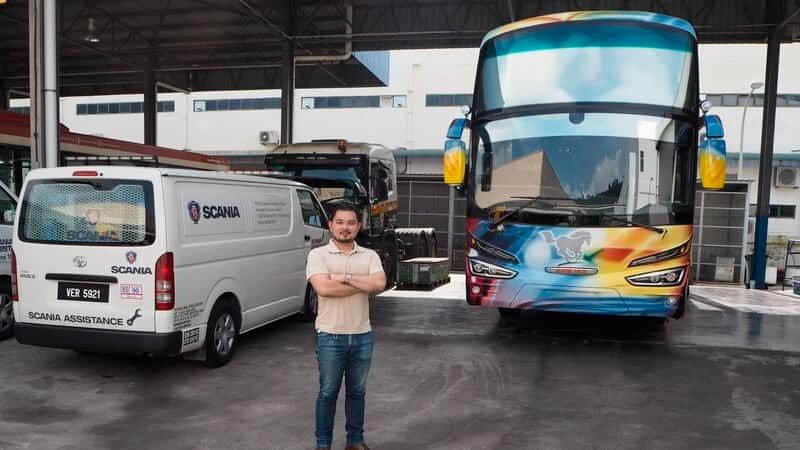
Today’s operations require vehicles to offer as much uptime as possible. On one hand, the biggest enemy of any bus operator is an unplanned breakdown, requiring the vehicle to be pulled in for repairs. Not only does this affect the bottom line, but also the reputation of the company as passenger may suffer delays and could be inconvenienced. Planned maintenance on the other hand, is helping to ensure that a vehicle is continuously providing the hours required on the road to turn a profit.
The service network of Scania in Malaysia is comprised of eight workshops in peninsular Malaysia and four in East Malaysia. Strategically placed, they offer operators fast turn-around and expert knowledge to get their vehicles back on the road. Although a very important aspect of running a bus fleet, the scheduled service intervals constitute downtime. Therefore, the location of the workshops is of great importance as the driving distance should be kept at a minimum. The scenic routes are reserved for the charter buses!
At each of the workshops, Scania’s teams comprise of technicians and specialists. For instance, dedicated staff is handling the parts warehouse: availability of parts is crucial for the swift turn-around of the vehicles. Using modern technology, each vehicle is being thoroughly checked before the service is carried out. Equipped with computers, technicians can accurately evaluate the status of all parts and decided if anything needs to be fixed in consultation with the client. Sometimes, it pays to have parts replaced a bit ahead of their intended lifespan in order to avoid the vehicle to come in for another service soon after. The availability of parts is guaranteed by the teams planning ahead on when a vehicle should be coming in for a regular service. Should parts be needed outside the recommended schedule, the central warehouses in Bukit Jelutong and Singapore feed the supply chain and even more uncommon parts can quickly be delivered to any of the workshops should the need arise.
Through Scania’s proprietary Fleet Management System connectivity and real-time vehicle data is ensured. By way of analysing the driving style of each driver, Scania offers proactive and preventive services to maximise uptime and operating economy. Scania’s approach to service and maintenance is reflected in the new slogan, which was present during the Malaysia Commercial Vehicle Expo 2022: “Profit Now. Profit Tomorrow.”
In the event of a break-down, Scania’s mobile teams will come to rescue the vehicle. Applying the same time rule of allowing two hours to respond and to get to the break-down site, the dedicated technicians are well-trained in maintenance in the field. Should a repair on site not be possible, the buses will be towed to the nearest workshop where they are being readied again for operation.
Although service intervals have been growing in terms of milage that a vehicle can drive before coming in for a service, it is not recommended to exceed the intervals as per indication by Scania. While such delays may impact the cash flow, the practice of extending service intervals also adds risks to the operation. As many components are interconnected, a faulty or worn out part can impact other parts which may then require premature replacement. Not expensing services in one week may quickly result in more money needing to be spent.
Workshops are more than repair shops: they can be career spring boards too. Having solid and profound knowledge of the vehicles can allow staff to move laterally in their careers. Knowing how to fix a bus for instance can be highly beneficial in designing it. Another aspect is that the act of servicing vehicles can yield data for the OEM on how to improve the design and functionality of the bus. All the more reasons to adhere to the service schedule as indicated by the manufacturer.